Pulver, Panscher und Pistolen
über Pulverbeschichtung, ABB und Sedotec
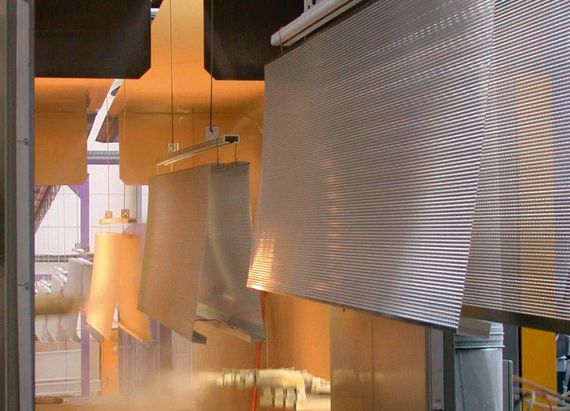
Die Veredelung einer Metalloberfläche durch Pulverbeschichtung ist seit Jahren als etabliertes Verfahren hinlänglich bekannt. Dennoch werden die Vorteile und Möglichkeiten des Pulverbeschichtens bei weitem nicht voll ausgeschöpft. Dass bestimmte Interessengruppen lieber die umweltkritische Nasslackierung im Vordergrund sehen, ist ein anderes Thema. An den Fakten jedenfalls geht kein Weg vorbei: Pulverbeschichtung ist wirtschaftlicher, schneller, beständiger und in beinahe allen Fällen der Nasslackierung überlegen. Nicht umsonst forschen Automobilkonzerne mit Hochdruck an der Pulverbeschichtung für ihre Produkte. Ein Plädoyer.
"Ein Auto, das mit Acryllack pulverbeschichtet wäre, können Sie nicht unterscheiden von einem konventionell lackierten Fahrzeug", behauptet Olaf Lederer. Und der Experte für Oberflächentechnik muss es wissen, schließlich kommt er von der Nasslackierung, ist aber "in den letzten Jahren zum Experten und bekennenden Fan der Pulverbeschichtung geworden." Seiner Meinung nach sei die Pulverbeschichtung hoffnungslos unterbewertet, gemessen an ihren Möglichkeiten. Denn gegenüber der Nasslackierung "ist das Pulververfahren schneller, billiger und haltbarer". Dabei würden Glanz und Brillanz dem Nasslack nicht nachstehen. Darüber hinaus gefährde es die Umwelt in keiner Weise. Lediglich die eingeschränkte Reparaturfähigkeit würde den "Durchmarsch der Pulverbeschichtung" verhindern.
Täglich gegen tief sitzende Vorurteile ankämpfen
Wie so oft sei es eine Kopfsache, meint Alexander Döring. "In den Köpfen der Menschen steckt nun Mal die Meinung, dass Pulverbeschichtung ein, bezogen auf den optischen Effekt, minderwertiges Lackierungsverfahren ist, geeignet nur für bestimmte Bauteile." Der Geschäftsführer der Firma Sedotec in Ladenburg arbeitet ständig gegen dieses Vorurteil an. Das Unternehmen, ein Spezialist für Blechbearbeitung, liefert mit seiner hauseigenen, hochmodernen Pulverbeschichtungsanlage täglich den Gegenbeweis. Nicht umsonst hat Sedotec für seine Anlage die Bahn- Zulassung, ein höchst selten vergebenes und qualitativ hochwertiges Gütesiegel, erhalten.
Bei der Pulverbeschichtung wird elektrostatisch aufgeladenes Kunststoffpulver auf metallisch leitende Werkstücke gesprüht, das dadurch haftet. Leichtmetalle wie Aluminium können durch eine entsprechende Behandlung vorbereitet werden. Durch die anschließende Erhitzung im Ofen auf 150°— 200°C schmilzt das Kunststoffpulver und vernetzt sich zu einer dauerhaften und dekorativen Oberfläche. Typische pulverbeschichtete Teile sind zum Beispiel Schaltschränke, Heizkörper, Hausgeräte, Maschinenverkleidungen oder Tischuntergestelle. "Aber auch Gabelstapler, Traktoren und viele Autoteile, wie Alufelgen, Fahrwerksteile oder anderes sind heute komplett pulverbeschichtet. So werden die Dachrelingteile vieler Kombis mit diesem Verfahren zu Hochglanz gebracht", weiß Lederer. Sowohl die funktionalen als auch die optischen Eigenschaften der Pulverbeschichtung halten jedem Vergleich mit nass lackierten Oberflächen stand.
1.000 Stunden in der Salz-Nebel-Hölle
"Pulverbeschichtete Oberflächen sind von höchster chemischer und mechanischer Beständigkeit, wenn beim Verfahren auf Qualität geachtet und die Vorbehandlung sehr gründlich durchgeführt wird", betont Döring. Der Korrosionsschutz sei extrem gut, die Oberfläche außerdem kratz- und schlagfest, chemikalienbeständig witterungs- und abriebfest und platze beim anschließenden Verbiegen des Werkstücks nicht ab. Sogar kleine Unebenheiten im Metall lassen sich überdecken. Darüber hinaus ist die Schicht bei Verwendung von Polyesterharzen UV-beständig, ohne dass ein Klarlack aufgetragen werden muss. Und auch bei der Optik müssten heutzutage keinerlei Abstriche mehr gemacht werden, begegnet Döring einem weiteren hartnäckigen Vorurteil. "Es sind eigentlich alle Farben und Oberflächenqualitäten sowie auch Metallictöne möglich. Für einen Kunden in London, der im RAL-Farbsystem nicht fündig wurde, haben wir ein Teil auch in British-Standard lackiert."
Mit verschiedenen Prüfungen lassen sich pulverbeschichtete Werkstücke gnadenlos auf Qualität und Beständigkeit testen: 1.000 Stunden im Salz-Sprühnebel-Test muss der Lack klaglos aushalten, damit die Bahn ihr begehrtes und sehr selten vergebenes Zertifikat erteilt. Selbst Premium Automobilproduzent Daimler-Chrysler verlangt in seinem Pflichtenheft nur 504 Stunden. Beim Traktorenhersteller John Deere sind es 480 Stunden. Neben dem Salz-Sprüh-Test können auch der zehnstündige Dieselkraftstoffbeständigkeitstest wie bei Unterbodenteilen für Daimler-Chrysler oder der 96-stündige Ölbeständigkeitstest wie zum Beispiel bei tragenden Teilen für Traktoren von John Deere zur Anwendung kommen.
Selbst begrenzendes Verfahren ohne Umweltgefährdung
Der Farbanteil bei Pulverlacken beträgt 100 Prozent und ist damit viel höher als der 30-60-Prozent-Anteil bei den Nasslacken. Der Anteil bei Nasslacken variiert, je nachdem ob es ein Wasserlack, Lösungsmittellack oder High Solid Lack ist. Pulverlacke enthalten darüber hinaus keinerlei umweltgefährdende Lösungsmittel oder Schwermetallanteile. Zusammen mit dem Pulverlack werden noch Bindemittel und Füllstoffe aufgebracht. Die Bindemittel enthalten einen Härter, sowie eine Kunstharzkomponente, das kann Acrylat-, Epoxid-, Polyester- oder Polyuretanharz sein. Erst wenn das Werkstück den Brennofen durchläuft, reagieren die Komponenten miteinander und es kommt innerhalb des Bindemittelsystems zu einer Molekülvergrößerung. Dadurch entsteht ein widerstandsfähiger Lackfilm. Das verwendete Lackpulver geht nun in eine duroplastische gleichmäßige Schicht von 50–120 µm über. "Welche Pulverart man verwendet, wird vom Einsatzzweck des beschichteten Teils bestimmt", erklärt Experte Lederer.
Aufgebracht wird das Pulver mit einer Sprühpistole. Zwei Systeme werden eingesetzt, um die Pulverteilchen in der Pistole aufzuladen. Beim Koronaverfahren sorgt eine in der Pistole integrierte Hochspannungskaskade für eine Aufladung. Tribo-Sprühpistolen arbeiten mit einer reinen Reibungsaufladung, die dadurch erreicht wird, dass das Pulver durch ein Kunststoffrohr geschossen wird. Zwischen dem geerdeten Werkstück und der Elektrode entsteht ein elektrisches Feld mit bis zu 100 kV Spannung, das die einzelnen Lackpartikel negativ auflädt. Da sich die gleich aufgeladenen Teilchen auf ihrem Weg von der Sprühpistole zum Werkstück voneinander abstoßen, verteilen sie sich in einer feinen Pulverwolke und schlagen sich gleichmäßig auf dem geerdeten Werkstück nieder. Lackteilchen, die am Werkstück vorbeifliegen, bleiben trotzdem im elektrischen Feld gefangen und schlagen sich auf der Rückwand des Werkstücks nieder. Der entstehende kleine Strom wird durch die Erdung des Werkstücks abgeleitet. Pulver, das sich nicht auf dem Werkstück niederschlägt, weil der Sättigungsgrad erreicht ist — das Verfahren ist selbst begrenzend — oder weil es aus dem elektrischen Feld entwichen ist, kann vollständig abgesaugt und wieder verwendet werden. Es entstehen — anders, als beim Nasslackverfahren — keinerlei umweltkritische Stoffe. Sammler, Abscheider oder eine Thermische Nachverbrennung sind nicht notwendig. Vor allem die ab nächstem Jahr noch schärferen Grenzwerte der seit 2001 gültigen VOC-Richtlinie, auch Lösungsmittel-Richtlinie genannt, können dem Pulverbeschichtungsverfahren nichts anhaben.
Wenn dann das aufgesprühte Pulver im Ofen getrocknet wird, müssen die Blechteile erhitzt und je nach Farbe 10–15 Minuten auf dieser Temperatur gehalten werden. Abhängig von Blechdicke und Teilegröße wird die Heizkraft des Ofens und die Transportgeschwindigkeit entsprechend berechnet und gesteuert. "Die Pulverbeschichtung ganzer LKW-Motorblöcke mussten wir kürzlich leider ablehnen, da die Zeit und der Energiebedarf zur Aufheizung auf 160° C zu groß gewesen wären", erläutert Döring Grenzen des Verfahrens. Doch inzwischen ist es mit Infrarotheizungen möglich, auch solche Anforderungen zu erfüllen.
Deutlich höherer Wirkungsgrad und bessere Wirtschaftlichkeit
Aber nicht nur unter Umweltbetrachtungen ist die Pulverbeschichtung im Vorteil. Das Verfahren ist deutlich schneller als die Nasslackierung, benötigt 30–50 Prozent weniger Material, da die Farbpartikel viel konzentrierter aufgesprüht werden, und das Material ist auch noch bis zu 50 Prozent günstiger, da keine teuren Lösungsmittel enthalten sind. Die Anforderungen an die Qualifizierung der Mitarbeiter sind geringer, da beim Pulverbeschichten, bedingt durch die automatische Sättigung am Werkstück und den Rücksprüheffekt, praktisch keine Fehler gemacht werden können. Nach einer kurzen Einarbeitungszeit können auch Ungelernte fehlerfrei lackieren. Alexander Döring von Sedotec bestätigt: "Unser Hauptprodukt, Schaltschränke für Maschinen und elektrische Anlagen, hat eine Durchlaufzeit von zweieinhalb Stunden. Beim Nasslackieren waren es vier Stunden, wobei zusätzlich noch 24-48 Stunden Aushärtung an der Luft hinzukamen." Die pulverbeschichteten Schränke lassen sich direkt nach dem Brennofen weiter verarbeiten. "Wir können sofort nach dem Abkühlen Türen oder Fachböden montieren und das Produkt versandfertig stellen", berichtet Döring. Und auch Lederer erzählt von LKW-Ladebordwänden, "die von zwei Mitarbeitern in sechs Minuten beschichtet sind, wo das Nasslackieren mit Schleifen, Vorgrundieren, Zwischenlüften und Decklackieren fast 30 Minuten erfordert."
In einem Zug zur gewünschten Oberfläche
Das Entscheidende sei aber die beim Pulverbeschichten in einem einzigen Vorgang auftragbare Schichtdicke von 50-120 µm. "Das bekommen Sie beim Nassverfahren niemals hin", so Lederer vehement, "pro Durchgang sind maximal 20 bis 30 µm Schichtdicke möglich." Deshalb müsse man häufig mehrmals lackieren, was die Verfahrenszeit weiter verlängert. Die oben erwähnten Dachrelingaufbauten für PKW müssten beispielsweise im Nassverfahren viermal lackiert werden, um die gleiche Beständigkeit und Güte wie bei einem Durchgang Pulverbeschichtung zu erhalten. Durchgeführt werden können beide Verfahren auf den gleichen Anlagen, sodass die Investitionen sich nicht unterscheiden. Lederer berichtet sogar von Anlagen, die sich umschalten lassen und auf denen beide Verfahren möglich sind.
Profis von Panschern unterscheiden
Da der eigentliche Beschichtungsvorgang mit Pulver keine Fehlerquellen in sich birgt, fehlerhafte pulverbeschichtete Teile aber nicht ausgebessert werden können, liegen die qualitätsentscheidenen Merkmale in der Vorbehandlung des Werkstücks. "Und hier unterscheiden sich Profis von Panschern", bekräftigt Lederer. Döring bestätigt, dass "bei uns das Hauptaugenmerk auf der Vorbehandlung liegt." So werden Bleche bei Sedotec in sechs Stufen vorbereitet, bevor Pulver aufgesprüht wird. Zunächst wird vorentfettet, entfettet, zwei Mal mit voll entsalztem Wasser (VE-Wasser) gespült und dann eine rund 20 µm starke Eisen-Dickschicht-Phosphatierung als Konversionsschicht aufgetragen und getrocknet. "Durch die beiden Entfettungs- und Spülbäder erhöhen wir den Wirkungsgrad signifikant und arbeiten mit konstant hoher Vorbehandlungsqualität." Die Schaltschränke für die Bahn sind aus Gewichtsgründen aus Aluminium und werden chromfrei passiviert, damit die Pulverschicht entsprechend haftet. Die hohe Qualität der Anlage und der Ergebnisse wird regelmäßig sichergestellt, indem die Werte der Bäder zur Vorbehandlung täglich gemessen, geprüft und vom Verantwortlichen mit seiner Unterschrift bestätigt werden. Ebenso wird die Schichtdicke regelmäßig vermessen und so genannte Ofenkurven erstellt.
Gerade die Vorbehandlung werde oft vernachlässigt. Damit ein pulverbeschichtetes Werkstück später nicht oxydiert und die Oberfläche keine Blasen bildet, wird es zunächst mechanisch und danach chemisch gereinigt und entfettet. Durch die anschließende Gelb- oder Grünchromatierung bei Aluminium und bei verzinktem Stahl sowie die Eisen- oder Zinkphosphatierung bei Stahl, bildet sich eine Konversionsschicht, die später vor Korrosion schützt. Gleichzeitig vergrößert sich dadurch die Oberfläche des Werkstücks, der Lackfilm haftet deutlich besser. Wegen besserer Umwelteignung sind inzwischen auch chromatfreie Methoden immer stärker auf dem Vormarsch. So sind neu entwickelte nanokeramische Beschichtungen deutlich leistungsfähiger, weniger aufwändig und umweltfreundlicher als herkömmliche Phosphatierungen.
Qualitätsanbieter haben Wechselkabinen
Welche Vorbehandlung in welcher Güte durchgeführt werden muss, hängt von der späteren Beanspruchung des lackierten Teils ab. "Fehlerquellen in der Vorbereitung gibt es genug", weiß Lederer. Da würden die falschen Chemikalien verwendet, Standzeiten der Bäder überschritten, Trocknungstemperaturen nicht eingehalten, Chemikalien durch zu kurze Abtropfzeiten von Bad zu Bad verschleppt oder die Bäder nicht ständig überwacht. "Gerade regelmäßige Kontrollen sind unbedingt erforderlich und müssen schriftlich dokumentiert sein", rät der Experte. Nur so könne später die geforderte Oberflächengüte erreicht und gewährleistet werden.
An Farbtönen gibt es heute keinen Mangel mehr. Neben sämtlichen RAL Farben und Tönen sind auch die Farben anderer Systeme wie Munsell, NCS, British Standard, Sikkens, HKS oder Pantone und DB erhältlich. Selbst Metallicfarben lassen sich heute pulverbeschichten. Nicht ganz so einfach sind Mehrfarblackierungen, da beim Abkleben temperaturfeste Materialien verwendet werden müssen. Bei Farbwechseln muss die Sprühkabine sehr gründlich gereinigt werden. Qualifizierte Anbieter verfügen wegen besserer Gründlichkeit und Zeiteffizienz beim Reinigen über Wechselkabinen. Um einen aufwändigen Farbwechsel in kürzester Zeit durchführen zu können, arbeitet Sedotec mit zwei Multi-Color-Automatikkabinen. Während in der einen Kabine lackiert wird, kann die andere gereinigt und vorbereitet werden. Bei Farbwechsel werden die Kabinen, die auf Schienen laufen, einfach hinzu- oder weggefahren. "So geht ein Farbwechsel im Handumdrehen", erklärt Döring stolz.
Verfahren bei Konstruktion berücksichtigen
Besondere Anforderungen an Teile, die zur Pulverbeschichtung vorgesehen sind, gibt es grundsätzlich keine. Konstrukteure von Serienteilen sollten eine Aufhängung, ein Loch, oder eine Auflagefläche einplanen. Denn, "solange der Siemens Lufthaken nicht zur Hand ist, muss man eben Löcher für die Aufhängung oder Auflageflächen mitkonstruieren", meint Lederer augenzwinkernd. Bedenken sollten die Konstrukteure auch, dass das Wasser der Vorbehandlungsbäder abtropfen kann. Für die Teilegröße gibt es fast keine Einschränkung. Auch sehr große Teile können heute pulverbeschichtet werden. Für Einzelteile, Kleinserien oder sperrige Teile gibt es große Hand- und Automatikkabinen mit eigenen Kammeröfen. Sedotec beschichtet in solch einer Kabine zum Beispiel Teile bis 3.200 x 1.200 x 1.400 mm LxBxH. Die Grenzen sprengen würde zum Beispiel ein Rotorblatt eines Windrades. Auch ein kompletter LKW, der neu lackiert werden soll, zum Beispiel einer dieser individuellen Formel-1-Motorhomes, ließe sich nicht pulverbeschichten, denn die Reifen würden die Ofentemperaturen nicht aushalten. Dass aber in naher Zukunft die Rohkarosserie eines LKW bei der Herstellung komplett pulverbeschichtet wird, daran glaubt Lederer fest. "Denn wenn die großen Anstrengungen der Fahrzeugindustrie an die Verbesserung der Reparatur- und Ausbesserungsfähigkeit von Pulverlacken erfolgreich sind, dann ist der endgültige Siegeszug der Pulverbeschichtung nicht mehr aufzuhalten."